We provide market-leading handling equipment that has been tried and tested by operators in all industrial sectors. Explore our range of drum handling equipment as well as other popular manual handling units.
Drum Handling Safety, Tips and Procedures
Industrial 205-litre drums and barrels can weigh up to 350kg (772lb) when full, these weights are well in excess of the UK guidance on manual handling – the male and female upper limit is 25kg and 16kg respectively. With drum weights potentially being 22 times greater than guideline manual handling limits, these containers pose a severe health and safety risk to people who handle them.
For companies that use barrels and drums within their operation, drum handling safety should be an important part of the work culture. Employers must look at the risks of loading and unloading heavy drums/barrels and put sensible health and safety measures in place to avoid the need for hazardous manual handling.
In this post, we are going to discuss the current landscape, risks and recommendations surrounding incorrect drum handling and ways to improve drum handling safety during daily operations.

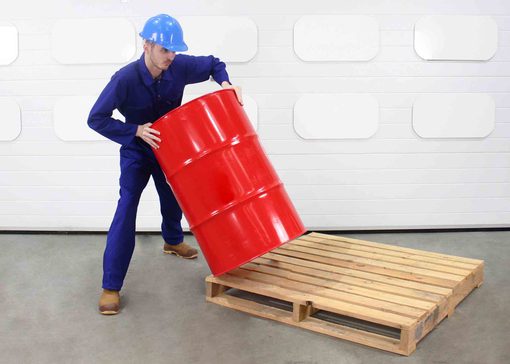
Drum handling safety challenges
- Many companies still ask staff to manually move drums and barrels, exposing them to the risk of injury and/or various musculoskeletal disorders (MSDs).
- Preventable workplace injuries are occurring daily in an age when drum handling equipment is readily available on the market.
- Some operators avoid using provided manual handling equipment, only to take legal action when they become incapacitated due to an injury.
- In certain scenarios poor-quality ‘safety’ equipment is used which is not fit for purpose and as a result, the injury still occurs.
- Many companies are unaware of the legislation surrounding manual handling equipment and so place their employees and their business at risk by not ensuring safe drum handling within the workplace.
- It can be difficult for companies to know whether equipment available on the market complies with the Machinery Directive or allows compliance with manual handling guidelines; just because a piece of equipment is for sale on the internet does not mean it necessarily complies with any Directives or British Standards, or that an acceptable risk assessment can be written about the use of such equipment.
- The pushing, pulling and lifting forces operators exert when using drum handling equipment are often found to be in excess of recommended handling limits.
- In some cases, drum handling products are available on the market for purchase, without the required guarding being supplied.
- Electrical equipment designed for use in the workplace must conform to the applicable electrical regulations and be assembled by suitably qualified personnel.


Poor drum handling practices:
- Manually moving drums by hand, churning them from ‘A’ to ‘B’ by balancing the load on the bottom edge of the drum; the loads experienced can exceed 90kg resulting in strain to the body, poor posture also increases the chance of injury;
- Pulling or lifting drums manually from (or onto) a pallet using excessive force, there is the potential for strain injuries and finger entrapment;
- Dropping drums into the horizontal position by pushing or tipping them over, this uncontrolled action risks injury, a spillage or spark creation in an ATEX area;
- Two-person drum tipping with one person holding each side of a heavy drum;
- Decanting drums/loading racking with a forklift by lifting them up in the horizontal orientation, drums can slide off the ends of the forks causing damage or injury.
Common injuries caused by unsafe drum handling:
- Broken or crushed limbs (particularly lower legs) when churning full drums and they fall hitting the employee;
- Bruised, broken or fractured fingers/hands following entrapment between drums on a pallet;
- Wide-ranging musculoskeletal disorders as a result of long-term improper handling of heavy loads, often involving the spine/back, shoulder or neck.
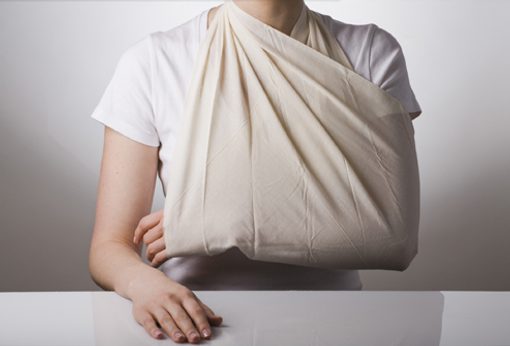

Recommended PPE to handle drums safely:
- Safety footwear should always be worn;
- Hard hat - if lifting loads at or above head height;
- Chemical resistant work gloves - if handling hazardous substances;
- Protective safety goggles - if decanting chemicals which have a potential to splash;
- Respirator - if decanting materials that give off noxious vapour or dust.
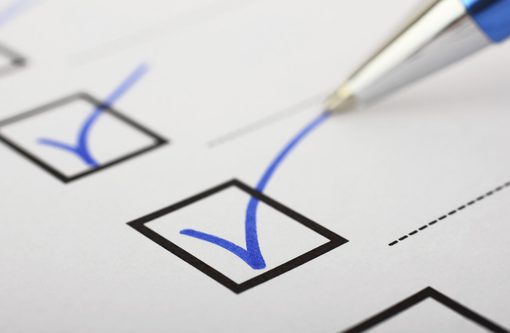

How to improve workplace drum handling safety
Drum Moving
- Before moving, check the drum for damage and ensure the bung/lid is securely fastened.
- Wear appropriate PPE, drums of hazardous chemicals may be coated in dangerous residues.
- When moving drums from ‘A’ to ‘B’ ensure the pathway you plan to take is clear and free from debris.
- Ensure the drum trolley being used is in a good condition and is designed to handle the specific drum-type being handled; some drum trolleys cannot handle plastic open-top drums, luckily our unique drum trolley can handle plastic drums with ease.
- Do not attempt to move drums up and down steep slopes with manual equipment not intended for the application.
- Operate drum hand trucks with a straight back using two hands and your leg if required by the design of the trolley; ensure no one is standing close to the load during manipulation.


Drum Lifting
- When lifting drums from (or onto) a pallet always use fully-tested drum lifting equipment suitable for the task, keep hands and other personnel clear of the drum when the lifting action is being carried out.
- Check the safe working load (SWL) of the drum lifter is suitable for the weight of drums being handled.
- Ensure the connection between the drum and the lifter is secure, if in doubt lower the drum back down.
- When transporting a drum using a drum lifter keep the load as close to the ground as practicable in case it becomes detached for any reason.
- Do not keep drums in a raised position when leaving the machine unattended for any length of time.
- When lowering drums down onto the ground ensure that no cables or hoses get trapped beneath the drum, equally ensure pallets are in a good condition before loading heavy drums onto them.
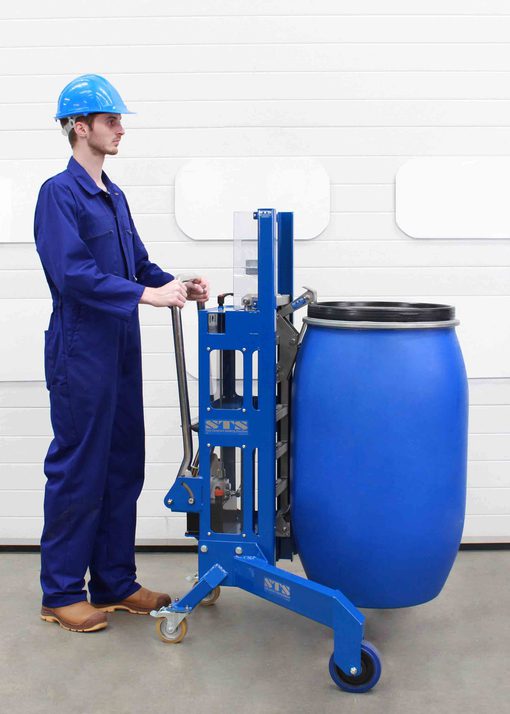

Drum Tipping
- Ensure drums are securely affixed to the drum tipping machine before raising up to height; personnel should not stand in front of the drum rotator during lifting operations.
- Drum tipping units should only be moved at slow speed when loads are raised to full height, this is due to the reduced stability of the unit in this condition.
- Ensure you can see where you are tipping the contents of the drum, if required ask a second member of staff to provide guidance from a safe secondary viewing location.
- The receiving vessel or container should have a large enough hole to receive the drum contents, consider using a large funnel, drum tap or another device to prevent costly spillages.
- Only keep drums in the raised position while decanting, once complete gently lower drums back down to the ground.
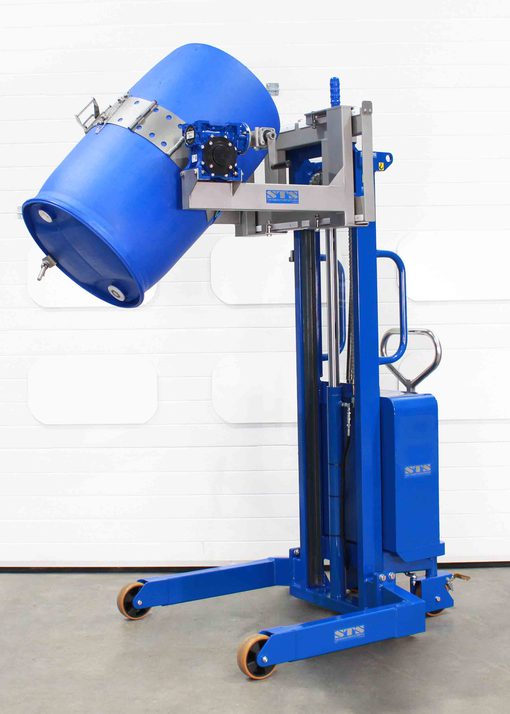

Drum Mixing
- Safety guarding should be fitted around all drum mixers to comply with the Machinery Directive 2006/42/EC, when the gate/door is opened the drum mixer must stop running immediately.
- Load all drum mixers with an appropriately specified drum lifter.
- Before mixing, check the drum for damage and ensure the bung/lid is securely fastened; lid seals should be checked to ensure they are in a good condition.
- Secure the drum into the mixer using the correct arrangement as specified by the manufacturer.
- Ensure the settings for speed control and mix duration (if present) are adjusted correctly before mixing is started.
- Power cables or air supply hoses should be routed to avoid them being a trip hazard.
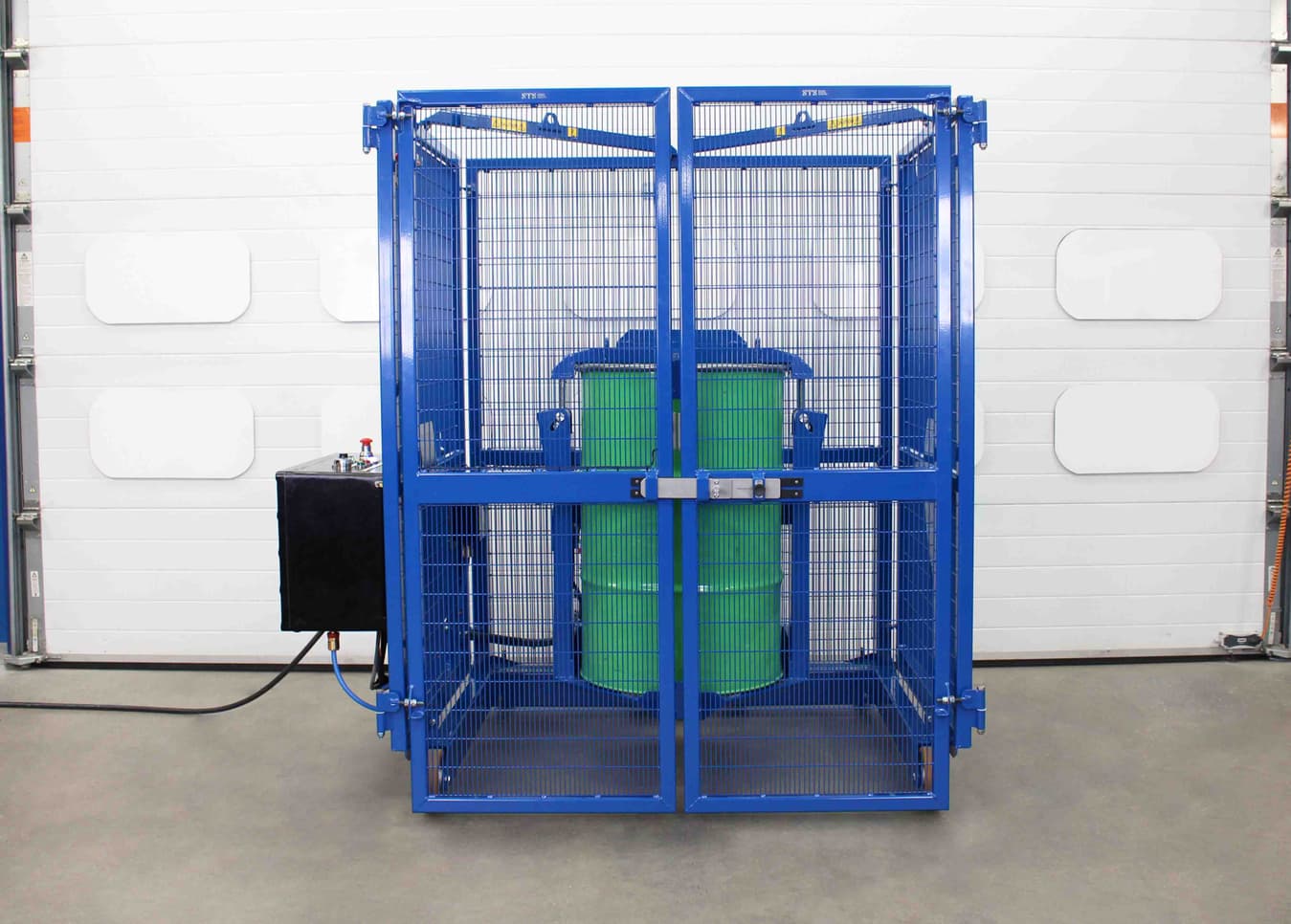
ATEX drum handling safety
Handling drums in an explosive area poses an additional set of risks and safety concerns. The following points are things to consider when using and/or sourcing ATEX drum handling equipment.
- Ensure earthing chains are fitted to mobile equipment and are in contact with the ground; depending on the application utilise earthing clamps to ground equipment and avoid a build-up of static electricity.
- Large sections of plastic and other man-made materials should be anti-static or conductive; this eliminates the build-up of static energy which could generate a spark.
- Mild steel drums will rust over time, as steel rusts the chance of a drum creating a spark when moved increases significantly; use drums that are in a good condition (no rust) and do not allow them to be dropped or driven into with forklifts or other equipment.
- Stainless steel is much less prone to creating sparks due to the material composition and characteristics (it can still spark under the right conditions). Use stainless steel to protect mild steel corners or edges and reduce the risk of mild steel on mild steel contact (high chance of spark generation).
- Bolts, nuts and other protruding articles should be made from stainless steel as opposed to mild steel, again to reduce the chance of spark generation.
- Wheels used in hazardous areas should be anti-static and/or have some method of dissipating any electrical charges which are generated.
Many safe working practices which apply to drum handling also apply to other areas of workplace health and safety. As such we have also detailed below some general health and safety recommendations that should be adopted in the workplace.


How to improve general workplace safety
- Ensure the workplace is clean, tidy and well illuminated. Staff should be able to see what they are doing and should not easily trip or fall over objects left lying around.
- Manual handling training should be provided to all staff at regular intervals. The training should include specific manual handling scenarios which are experienced during normal business operations.
- Risk assessments should be completed, and any mitigation actions should be taken, thus reducing the overall risk of injury in the workplace.
- Employees should read all risk assessments and ensure they work in accordance with standard operating procedures (SOPs).


Products
Contact Us
Do you have a manual handling issue we could solve? We’d be happy to discuss any handling concerns and advise on the most suitable STS equipment. You can talk to us via telephone, email and social media.