Do you have a manual handling issue we could solve? We’d be happy to discuss any handling concerns and advise on the most suitable STS equipment. You can talk to us via telephone, email and social media.
Stainless Steel Drum Handling Equipment
We specialise in the development and production of a wide variety of stainless-steel drum handling equipment suitable for sectors of industry that require units with a smooth unpainted finish that can be easily cleaned; our offering includes an assortment of stainless steel drum lifters, trolleys, dollies and tippers.
We have the knowledge, experience and expertise to design and manufacture stainless steel products that meet food, pharmaceutical and cleanroom standards. This page will identify the important factors to consider when sourcing a stainless steel drum handler; finding the correct product for your application is crucial and we can help you achieve this.
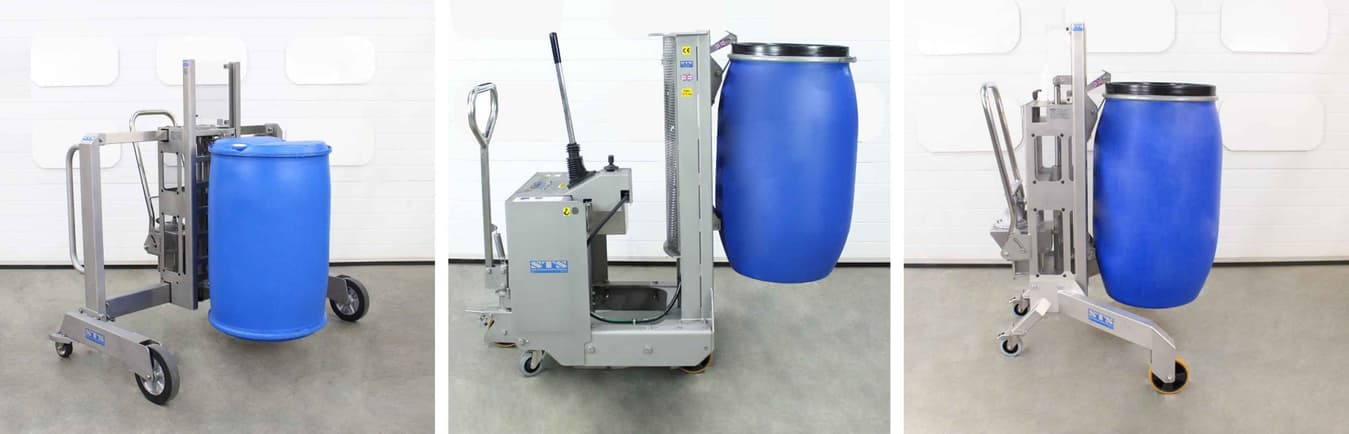
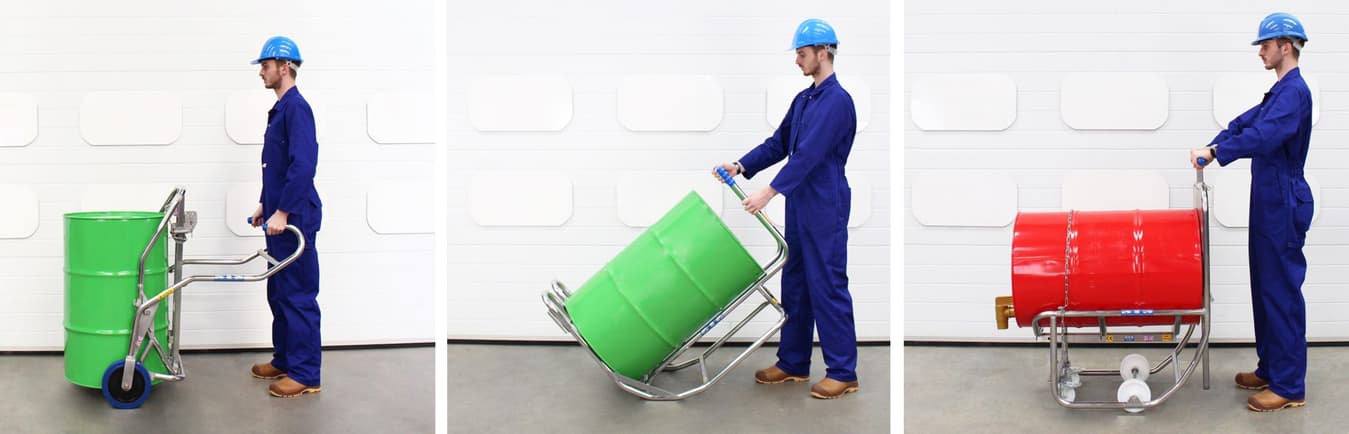
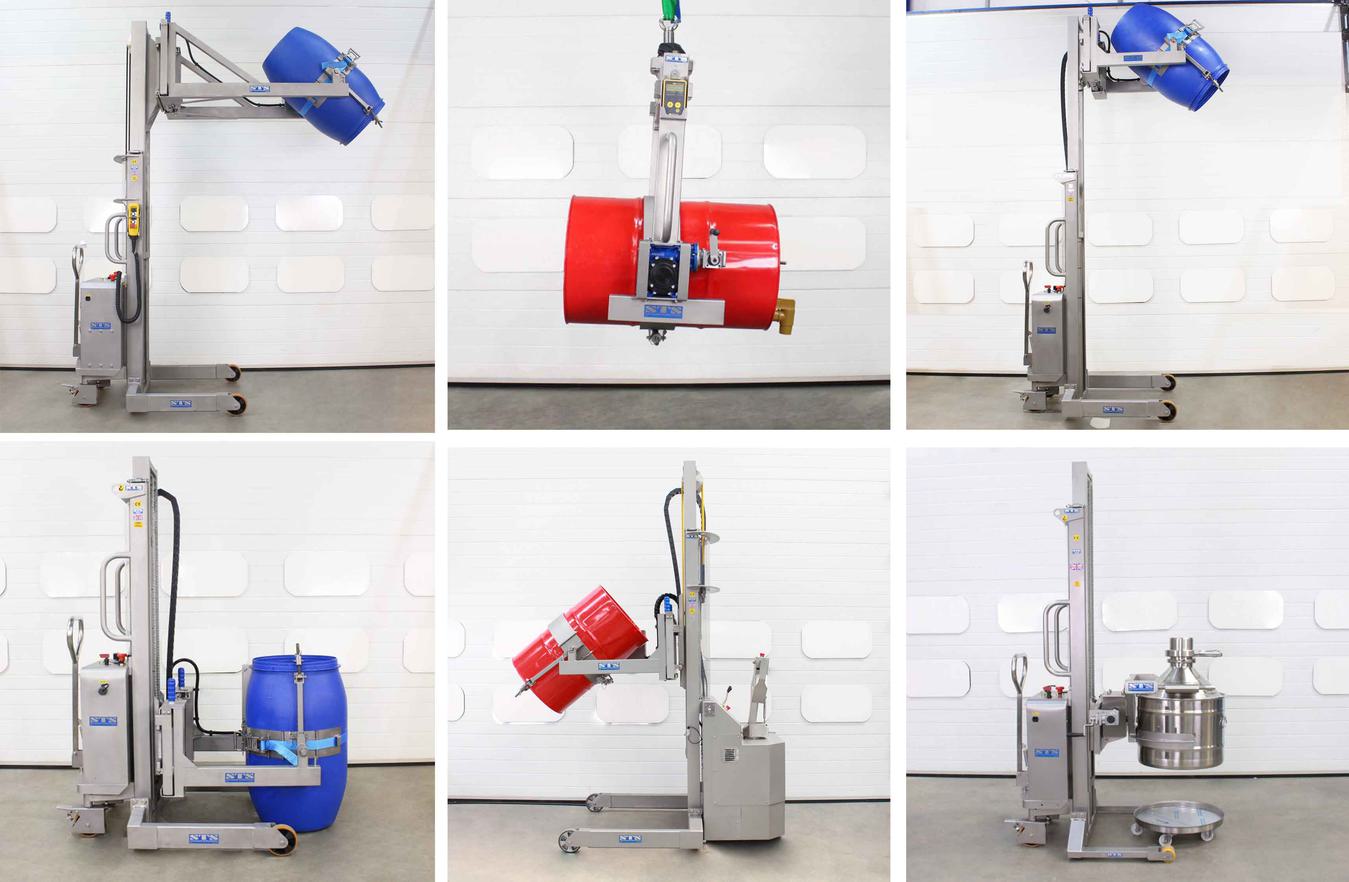
Considerations when searching for stainless steel drum handling equipment
If you have a requirement for handling steel, plastic, or fibreboard drums within a clean room, pharmaceutical area or food-grade process area you may consider sourcing a stainless steel drum handler. There are several aspects you will need to consider:
- Is the unit contained and easy to clean so operators can avoid cross-contamination between processes?
Our units are designed to be open and accessible, allowing cleaning with a damp cloth. Lifting channels and linear components are not hidden allowing debris to be easily removed.
- Does the unit require frequent maintenance and can any work be carried out easily?
Quality components with adequately specified duty cycles make for robust systems. Our drum-handling products are used globally and rarely require replacement spare parts. We supply drawings when required of parts and sub-assemblies to make maintenance easy, facilitating minimal downtime.

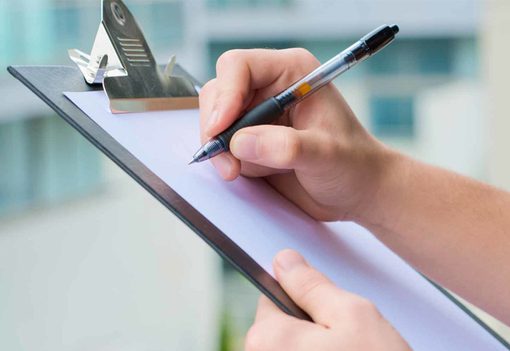
- Will equipment survive use in a harsh corrosive environment?
Made from 304-grade stainless steel, every INOX unit we manufacture is designed to be used 365 days per year in all industrial settings.
- Will the unit help to speed up processes, therefore, increasing efficiency?
Powered equipment is always preferable to using manual equipment and preferable to man-handling drums. Labour is one of the largest costs to any business, any machine that reduces the time it takes to complete a given action has the potential to offer an ROI (return on investment) in the form of efficiency gains.


Low contamination risk
One of the most important aspects to consider when evaluating a piece of stainless steel machinery for your process area is the ability to easily clean down the unit. We construct all our cleanroom units from 304-grade stainless steel and finish the metal to ensure it has a smooth clean finish - operators can easily clean and disinfect the unit between uses.
Manufacturing in stainless steel removes the risk of any contamination from paint chippings; the smooth clean finish makes it ideal for food processes and/or pharmaceutical applications. If you do not have a requirement for stainless steel we also offer mild steel drum handling equipment which is grit-blasted and powder-coated.
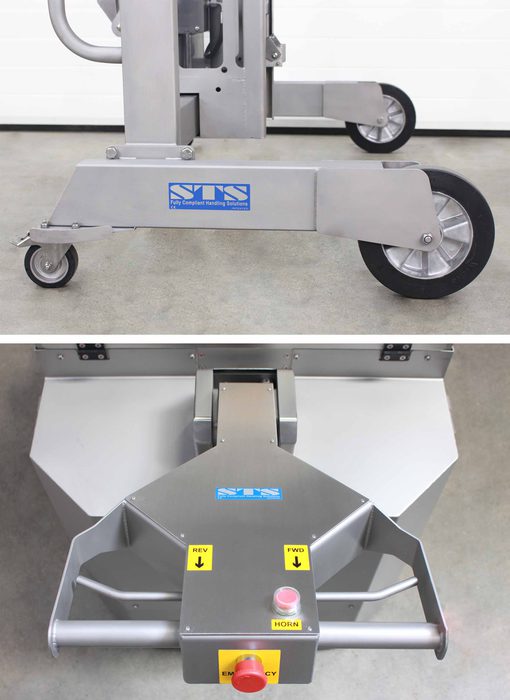

High quality manufacturing
Here at STS, we pride ourselves on manufacturing high-quality drum handling equipment that is durable and very low maintenance. We expect units to be used 7 days per week, 365 days per year and as such, we design them with longevity in mind. We use accelerated life testing to analyse the longevity of our products, this ensures they are robust enough to deal with daily tasks and that they last decades, not just years.
We source premium parts by working with expert suppliers across the UK, Europe and North America. Our team of engineers tests and inspects every unit upon completion of manufacture to ensure zero defects. If customers require spare parts or encounter a technical issue our team can offer industry-leading advice and support as soon as required.
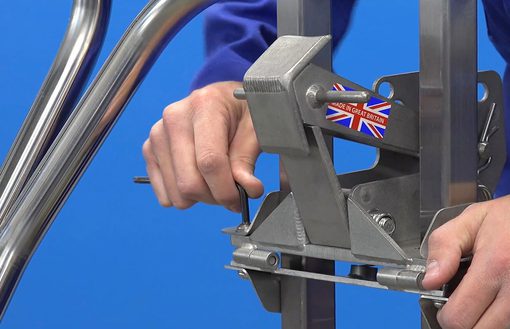

Improvements in efficiency
For operators working in regulated working environments, processing materials can sometimes be slow due to safety and contamination considerations. Efficiency can be improved through the use of safe drum-handling equipment. We can customise our drum handling units to suit specific customer requirements and to help optimise production flow. Please see below some of the optional features that we have installed on our machines to help improve efficiency for our customers:
Load cell system - With our load-cell system you can weigh drums while you handle them, this is ideal for batch manufacture where measuring material quantities is vital.
Power drive system - When handling a high volume of drums and travelling long distances, powered drive systems can be added to remove all manual handling.
Bespoke unit - We can design and adapt our units, adaptions include height, width and safe working load.


Stainless steel drum handling equipment features
Our qualified team of engineers has over 24 years of experience manufacturing stainless steel drum handling equipment for all areas of industry; each design is reviewed via a multi-tier checking regime. We include the following features on our machines:
Nickel/zinc-coated hydraulic rams - we utilise a strong long-lasting nickel/zinc coating on our hydraulic rams. This makes the parts corrosion-resistant and well-suited to wet food areas or cleanroom environments.
Shrouded hydraulic pumps - on our manual-lift machines we use UK-made hydraulic pumps to raise the load. This manual pump is housed within a stainless steel enclosure to protect it.
Food-safe lubrication - for customers working in food environments we coat clevis pins, joints and other moving parts with food-safe grease to reduce the chance of corrosion.
Electrical connections - we coat all internal electrical connectors with a contact protector to ensure the connections are not compromised in harsh environments. External connections are made in IP-rated connectors where required.
Polycarbonate guarding - as part of our design process we ensure all our stainless steel drum lifters and tippers have the correct guarding in line with the Machinery Directive.

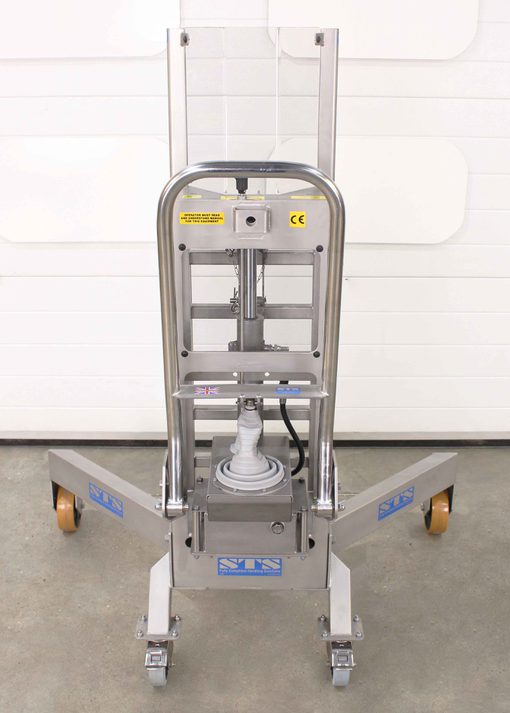
Fabrication and metal finishing processes
Stainless steel parts are segregated from mild steel components during manufacture; different benches and tools are used when working with stainless steel. We use the latest TIP TIG machines with semi-automatic wire feeds to weld up our stainless steel drum handlers, the powered wire feed element of the machines accelerates the fabrication process.
Stainless steel parts are finished in two main ways:
- Vibratory polished - Welded parts are electrochemically etched before being placed in a large vibratory polishing machine. This process deburrs parts and polishes the surface to leave it smooth and shiny.
- Polished and etched - materials are polished or buffed by the fabrication team; once welded we then use an electrochemical process to remove contaminants from the welds and return the stainless steel to a bright and clean condition.
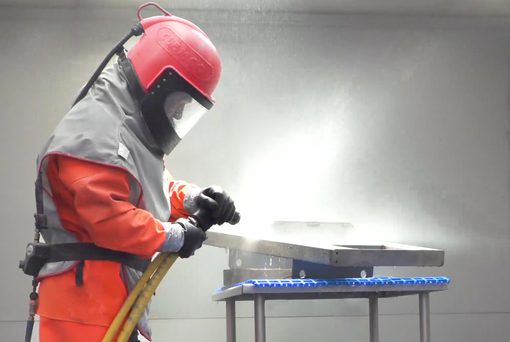
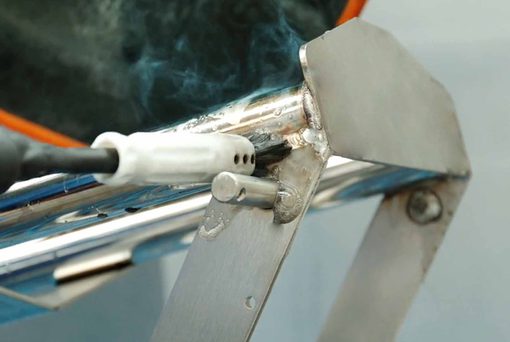
What industries do we work with?
We work with a wide range of healthcare, pharmaceutical and food companies.

The STS kit provided me with a lot of confidence and was easy to use in our environment.
The unit has proven itself to be well manufactured, robust and long-lasting.
It’s by far the best piece of engineering that we have ever had on site. Solid, safe and practical – I wouldn’t want to go back to moving them with brute force again.
Contact Us
Products
We provide market-leading handling equipment that has been tried and tested by operators in all industrial sectors. Explore our range of drum handling equipment as well as other popular manual handling units.